Ever wondered what happens during a re-pad?
October 11th, 2024
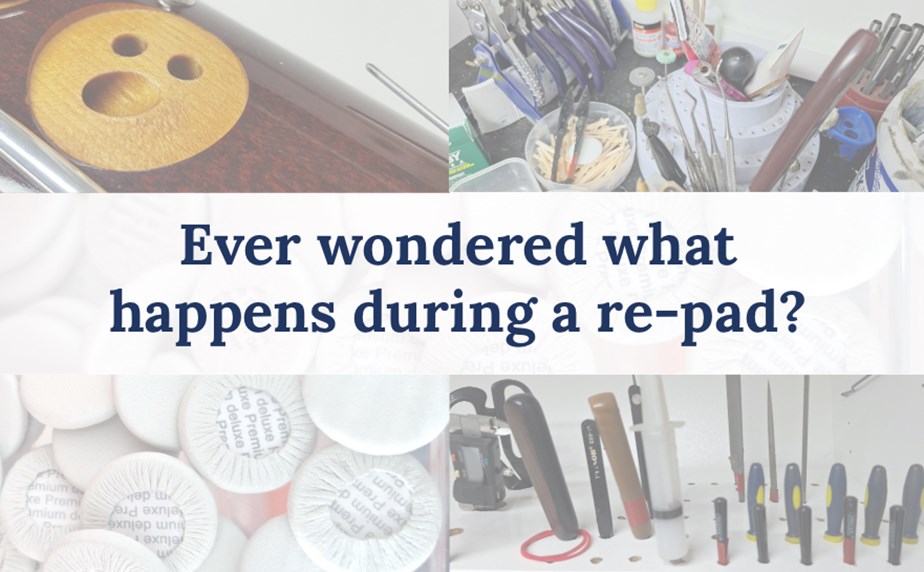
The mechanics of the bassoon are complex compared to many instruments. Getting all of the moving parts to work in tandem with each other takes years of experience, and an encyclopaedic knowledge of the instrument.
So, what happens during a bassoon re-pad?
Regulating the keywork
The average bassoon has around 50 pieces of keywork, which if lined up end to end would stretch around 5 metres.
During a re-pad or service, the position, angle and height of each of these keys needs to be carefully balanced, to ensure each of the pads open and close the right amount, in the right place, at the right time.
This keywork balancing is called regulating the keywork, and a bassoon with poor regulation will not play as it should - or at all if it’s really bad - which is why regulation is an integral focus during a re-pad or service.
If a pad is out of place because of a bent key, for example, it won’t seal the tonehole, and so that note and other notes on the instrument will play out of tune or not sound at all.
A bent key is fairly easy to spot, but the leaks that occur because of poor regulation are almost impossible to see easily by eye.
A cork that is too compressed, a felt that has slipped, a pad with an indentation, a spring which is too weak – all of these issues, and many more, will cause leaks that affect how the bassoon plays.
All of these leaks naturally develop over time, and lead cumulatively to a bassoon which is hard to blow, stuffy, too quiet, and out of tune.
Cleaning work
One of the sometimes-overlooked tasks in servicing or re-padding a bassoon, is to thoroughly clean it. Perhaps surprisingly, cleaning a bassoon isn’t just a cosmetic task, although cosmetics are certainly a part of it. The cleaning work we do is, in fact, important for how the bassoon plays, as well as for preserving it for the future.
Over time, dirt, grease and the oils in our skin can get under the keywork. It can work its way onto the pads, making them sticky, or causing them to leak. The dirt that accumulates on the wood can start to degrade the finish, and even start corroding the plating on the keys. The grease in the key pivots also dries out over time, and needs cleaning out and re-applying.
This is why our re-pads always start with a thorough clean of the instrument.
On the inside, toneholes can get clogged with dirt, as can the u-bend and even the bore of the bassoon. Our servicing work helps maintain clear and clean airways.
Replacing the pads
The question about whether your bassoon pads need replacing depends entirely on the condition they’re in. Pads degrade naturally over time – they start off white, malleable and soft, which is perfect for forming a seal over a tonehole face. Over time, though, they start to go hard, which prevents them from sealing properly.
Pads which are turning yellow or brown may be coming towards the end of their useful life.
Bassoon keys have pad cups of varying depths, sizes and shapes - there is no industry standard across manufacturers, which is why we stock every possible size, thickness and shape of pad that is available!
Selecting the wrong thickness of pad can cause it to leak, whether it is too thick or too thin.
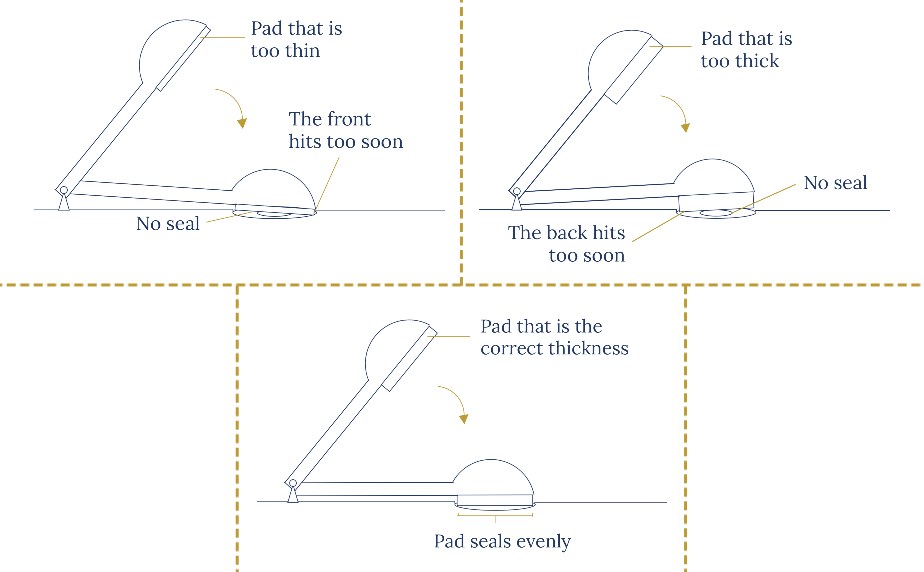
In addition to thickness, the shape of the pad also matters. The tonehole faces on a bassoon are normally domed, and many of the toneholes are angled towards the bore of the instrument. This combination, of domed faces and angled toneholes, creates a unique problem for the bassoon – the pads, which are manufactured flat, need to be carefully shaped around the tonehole faces to ensure they seal the tonehole.
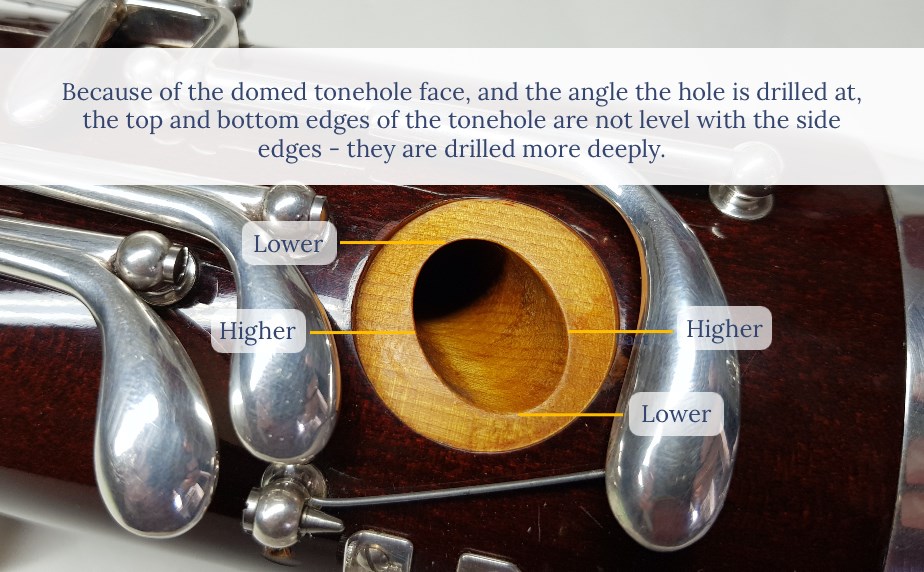
It takes years of experience to perfect the nuances of seating each pad correctly. During a re-pad we use a feeler gauge to feel the pressure on every part of the closed pad, and make tiny adjustments to ensure every side exerts equal pressure. With around 25 pads to fit, all fitted with heated adhesives, this is a significant undertaking.
Some bassoon manufacturers flatten the tonehole faces to mitigate the difficulties involved with padding domed toneholes.
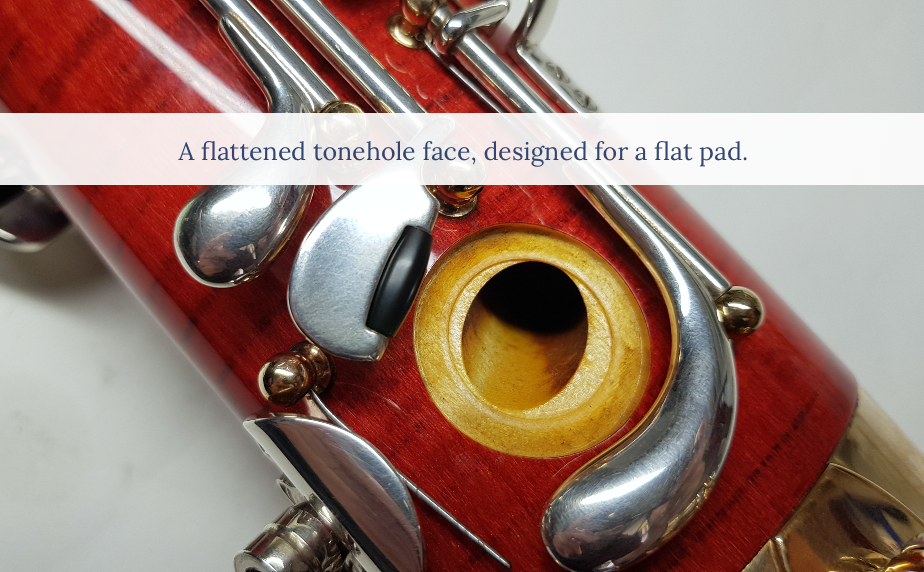
The dreaded A and Bb
There are two toneholes on the bassoon which are notoriously difficult to pad correctly, the A and Bb. This is because a single pad has to cover multiple toneholes on one tonehole face – achieving a perfect seal on each of them is a feat which takes experience and practice to accomplish.
During a re-pad, each of the toneholes needs to be sealed in its own right, and the repairer must know how to seat the pad so that no air can leak from one tonehole into another, or out of the sides of the pad itself.
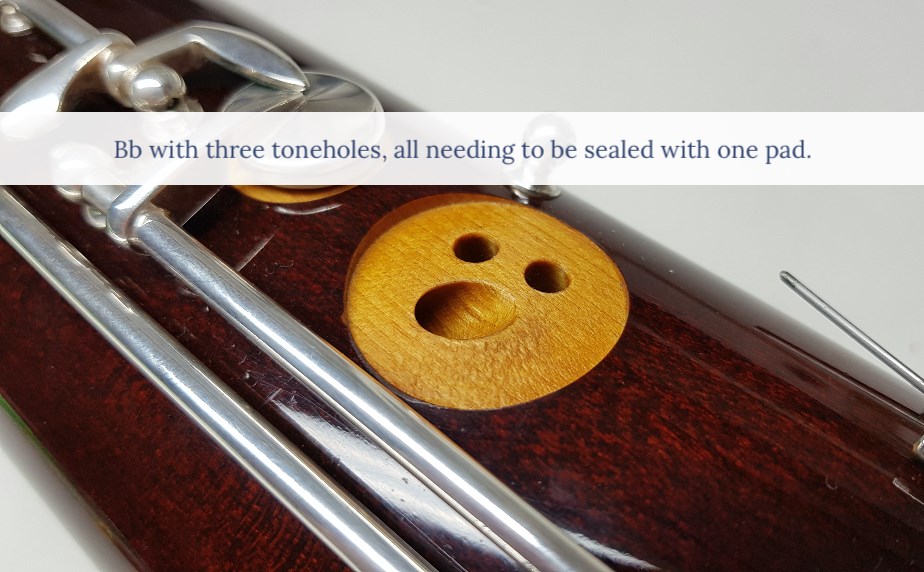
Tonehole condition
Once a bassoon gets to the point at which most of the pads need changing, there will usually be some wear to the faces – the sealant may have worn through, allowing air to leak through the wood itself (which is surprisingly porous). As it wears the varnish can also chip, causing gaps where leaks can occur, and the unvarnished wood grain can become rough, causing the surface to be too uneven to maintain a seal when a new pad is fitted.
The wood of the tonehole itself can also swell and become misshapen over time because of exposure to moisture. This leads to leaks from the pad and, if left untreated, more serious damage to the instrument itself. Some parts of the tonehole are more susceptible to moisture than others.
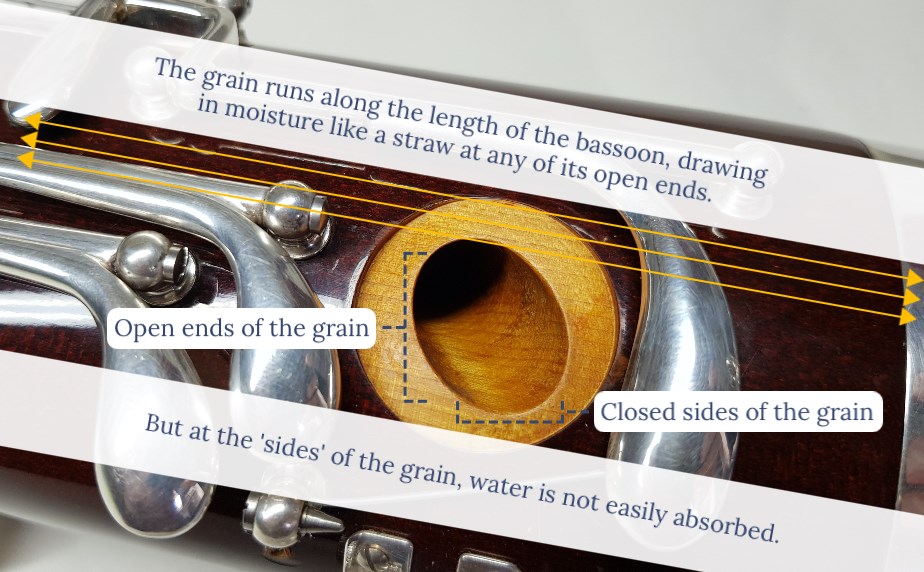
Where necessary, during a re-pad, we will scrape back the tonehole to its original dimensions, repair any damage, and re-seal it. In the worst cases we may even replace the tonehole face entirely. Trying to re-pad without fixing these issues is likely to result in leaks.
Vacuum & pressure testing
A tight seal is one of the main goals we try to achieve when re-padding a bassoon, and continual vacuum testing is undertaken to check each of the pads. At Double Reed we use a combination of mouth suction tests and mechanical pressure tests with a magnehelic gauge to check the seal.
Checking and play test
The final stage of a re-pad is checking the bassoon over thoroughly, and play testing it. If all is done correctly, the bassoon should play as well as it did when new (if not better).
If any of the elements of the re-pad are executed poorly, the bassoon may end up with tuning and intonation issues, an inferior tone, and notes which don’t speak easily when played. For this reason, it is important to always take your bassoon to a technician who specialises in bassoons, as many of the techniques used on other woodwind instruments are not transferable, and the bassoon takes special insight in order to re-pad correctly.
Does your bassoon need a re-pad? You can read more about our repairs service here. Contact us for specialist advice and we will be happy to discuss your needs.
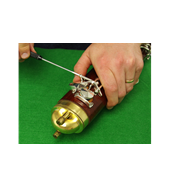
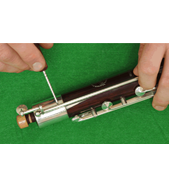
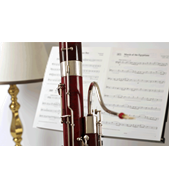
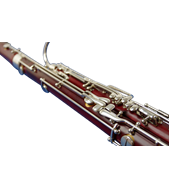
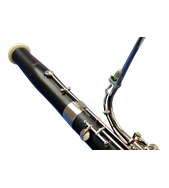
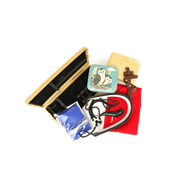